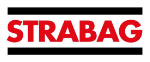
STRABAG AG
“Etschel Brunnenservice is the right partner for guaranteeing quality in our well construction and service.”
When a new well has been drilled, the work on the well is not yet done. The waterways are still closed to a large extent at this point, as drilling residues such as bentonite are still on the borehole wall.
In many cases, a regular layer forms around the well that can be several inches thick and only allows water to pass through in a few places. All the residue from the drilling process must therefore be removed before the well can be put into operation. The process responsible for the initial activation of the well is called well development.
A wide variety of methods are used to try to remove all residues from the well. The aim is to produce the maximum possible production capacity of the well. But beware: many water well development techniques used are not very effective and do not have the ability to remove the residues.
Especially in the non-visible area of the filter gravel and borehole wall, some methods have no effect at all. As a result, many wells can never reach their maximum possible production rate.
To truly clean a well in a sustainable, effective and deep way, a well development process is needed that removes virtually all drilling residues. Our High Pressure Impulse Process, or HPI Process for short, meets all the criteria of a modern development process and clearly outshines jetting technologies.
With our high performance rotary nozzle system MAXINOZ we achieve significantly better results than with all other well development processes known to us.
The HPI process removes even the hardest deposits up to the borehole wall without damaging the screen. This is achieved by rotating the two eccentrically arranged pairs of nozzles of the rotation unit in opposite directions at up to 7,000rpm using the recoil principle and generating a pressure of up to 8,000 psi. Due to the high pressure and speeds, the result is not a hard water beam but a mist.
The enormous forces of the rotating unit moving up and down in the well cause the gravel behind the screen to oscillate. The vibrations loosen all the deposits. Even the layer far away from the screen. At the same time, the technology sucks the solids into the well, as a strong negative pressure is created at the level of the nozzles.
A submersible pump, which hangs just below the upper edge of the screen, immediately suctions the dissolved substances out of the well. Outside the well, a measuring device is installed to determine exactly how many solids, sand and sludge have been discharged from the well.
Since all steps in this process are carried out simultaneously, the HPI process is not only highly effective, but also fast. An increased flow rate and an improved water quality is the consequence for the well operator.
A well development carried out with the HPI Process ensures a reduced maintance afterwards, as the well has been completely activated.
The operator can run his well at maximum increased flow rate and can expect a significantly extended well lifespan. He can select an energy-efficient pump that is precisely matched to the specific yield of the well. Electricity and energy can be saved and the intervals for future well rehabilitations will extend.
We have decades of experience in the well drilling, pump and well service industry and know the market since more than 100 years (starting in 1919 with a deep drilling company). With our know how and countless years of research, we exactly know the interaction of factors that are important to run a well at its maximum flow rate.
In the early 90´s, we recognized the need of good well rehabilitation methods. At this time it was common to clean wells with poorly performing methods like brushing, surge plugging or even chemicals. We had a great idea to bring a new, outperforming well development and rehabilitation method on the market and invented the HPI-Process.
After some years of research our technology performed very well and we developed it further and further. In 2007, after drilling wells for more than 88 years we decided to concentrate in the well development and rehabilitation industry only as the market was growing and our technologies were in high demand.
Our goal was to extend the lifespan of wells enormously and bring outstanding results regarding the performance and longevity of new and old wells. Today we aspire to have the worlds market leading technology and want to bring our know how into the whole world.
Emphasize Etschel Brunnenservice’s commitment to providing personalized solutions and expert consultation to clients throughout the entire well development process.
With surge plugging and partial desanding, it is estimated that 40 to 60% of the remaining filter cake can be removed. Almost 100% can be removed with the Etschel JET Master®.
This has been proven with old deep wells, which, on the occasion of subsequent developments, after treatment with the Etschel JET Master®, permanently showed a far better spec. performance (m³/h and meter drawdown difference).
Showcase of case studies and testimonials that demonstrate the effectiveness and efficiency of the JET Master System in various well development projects, highlighting Etschel Brunnenservice’s expertise in the industry.
The most common well development tools are brushing, sewer and jetting tools, low and high pressure applications, the use of chemicals and the HPI-Process.
HPI-Process powered by the JET Master can loosen the deposits, transport them out of the well and take measurements at the same time. With up to 8.000psi, It has much more power than other tools and thus a significantly higher depth effectiveness. It treats the well in one task and not in sections. The parameters of HPI-Process can be adjusted to every well diameter. HPI-Process can be used for all screen materials like PVC, steel, stone or even glued filter screens. It is a much faster process than other development tools as all work steps are done at the same time. HPI-Process is not generating a water beam like Jetting tools but generates high pressure impulses which brings the gravel to swing. The nozzles rotate with 7.000 rpm due to the recoil principle and not with an engine like other Jetting techniques.
We help the well operator to be able to use his well in a cost-efficient, sustainable and effective way after development. With our process, the HPI Process, we get the maximum production capacity out of the well. Thus, the well can be operated in a long-term, low-maintenance and energy-efficient manner.
In Germany, Etschel Brunnenservice is a service provider for water well development, rehabilitation and refurbishment. With over 100 years know how we can help our clients with our experience.
Internationally, we sell our technologies to partners worldwide who are interested in using market-leading technology for well development and rehabilitation to have satisfied customers and a competitive advantage.
Yes, we can adjust all parameters of our technology to the construction of the well. It is suitable for wells from 3” (DN80) to 48” (DN1200). It can be used in wells up to 3.000ft (1.000m). All common screens like Johnson type, bride slotted, PVC, wood, stone, glued filter screens can be threatened with HPI-Process.
This depends on the length of the casing / screen. A 150ft (50m) deep well is completely developed in approximately 2,5 hours. For a 1.000 ft (330m) deep well HPI-Process needs around 6 hours.